Rack Systems
Industry Mart can provide high-density rack systems to meet your specific storage requirements. Although static pallet rack is the most common rack storage option, it does not fit all storage applications. When space is a premium or when product flow is required, a high-density system like push-back, drive-in, flow rack, or carton or keg flow may be the right solution for you.
Let our experts consult with you to determine the best system option.
Pushback
Pushback rack is a high-density storage system that increases the total number of pallets, while providing more pick faces than traditional high-density storage systems like drive-in. Push back systems are available from 2 to 6 pallets deep per lane, and can be placed in a back-to-back configuration to total 12 pallets deep.
Pushback rack is ideal for both LIFO and FIFO systems, with up to 75 percent more storage capacity than a selective rack system.
Pushback rack combines the high density of drive-in systems and self-positioning features of flow rack. It offers the flexibility to store multiple SKU’s and eliminates aisles previously needed in a selective rack environment. Pushback is front loading/unloading, reducing the labor and operational costs of drive-in rack.
Pallet loads move on a series of nesting carts, and are gravity-fed forward on rigid structural steel rails, improving quick and easy access to a range of SKUs.
Pushback Features
- Loads “push-back” when loaded and slide forward when unloaded on telescoping / retractable trays
- High Density Storage
- Reduces total number of aisles
- Great where space is a premium such as freezers and coolers
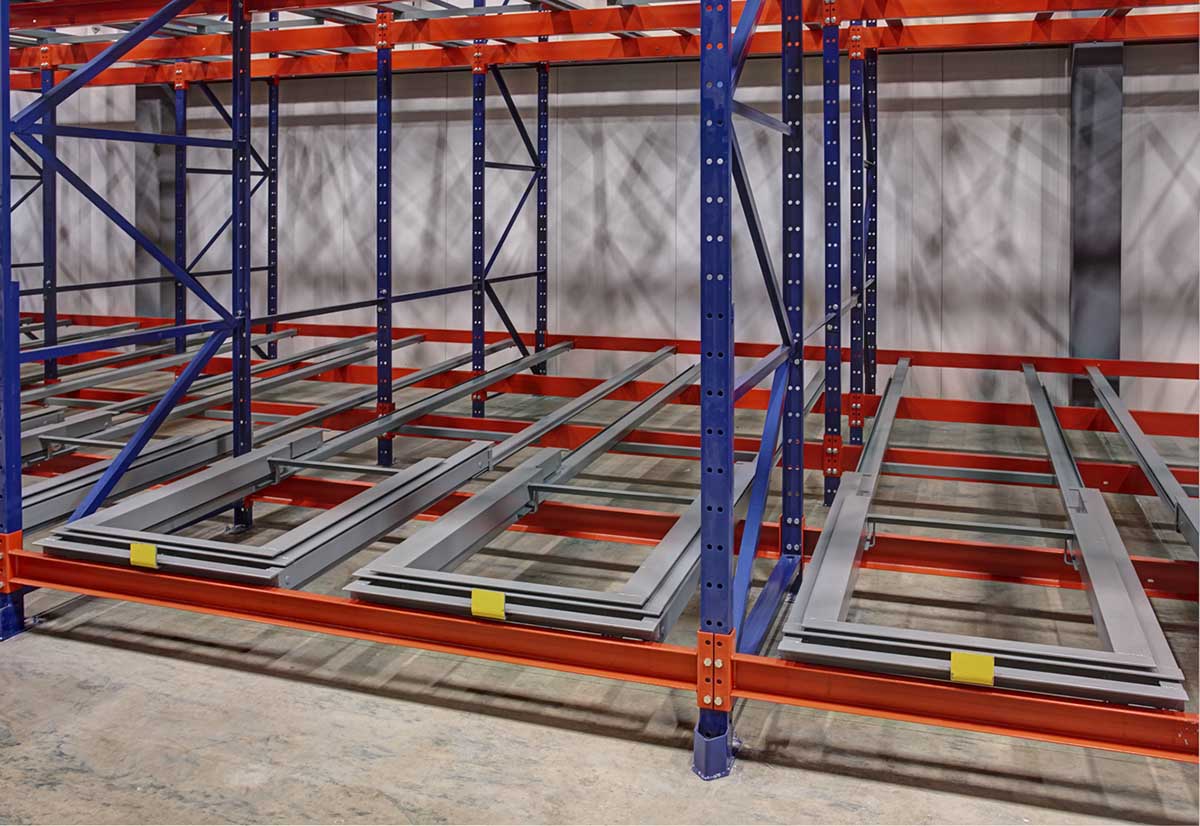
Drive-In
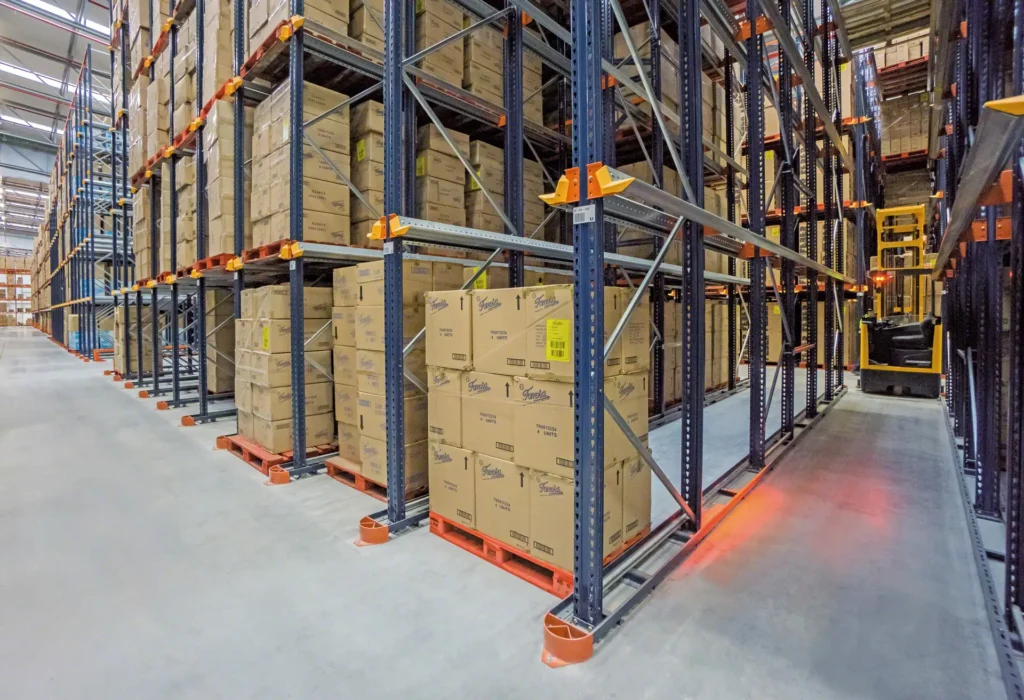
Drive-in rack is a high-density storage system where the forklift actually enters or drives into the rack structure. It is specifically custom-designed to fit your specific forklift as well as your pallet load sizes.
Drive-in rack is a Last-In First-Out (LIFO) application where multiple pallets of the same SKU are stored in depth, and where time sensitivity is not an issue. Drive-in rack eliminates the need for floor stacking and increases overall storage space.
Drive-In Features
- Last In / First Out (LIFO) Stock. Loaded and unloaded from the same end.
- Eliminates the need for more aisle space!
- Great for products that are not time / date sensitive
- Custom designed around your forklift and pallet loads
- Pallets stored on “rails” instead of beams
- Requires standardized pallets in good condition
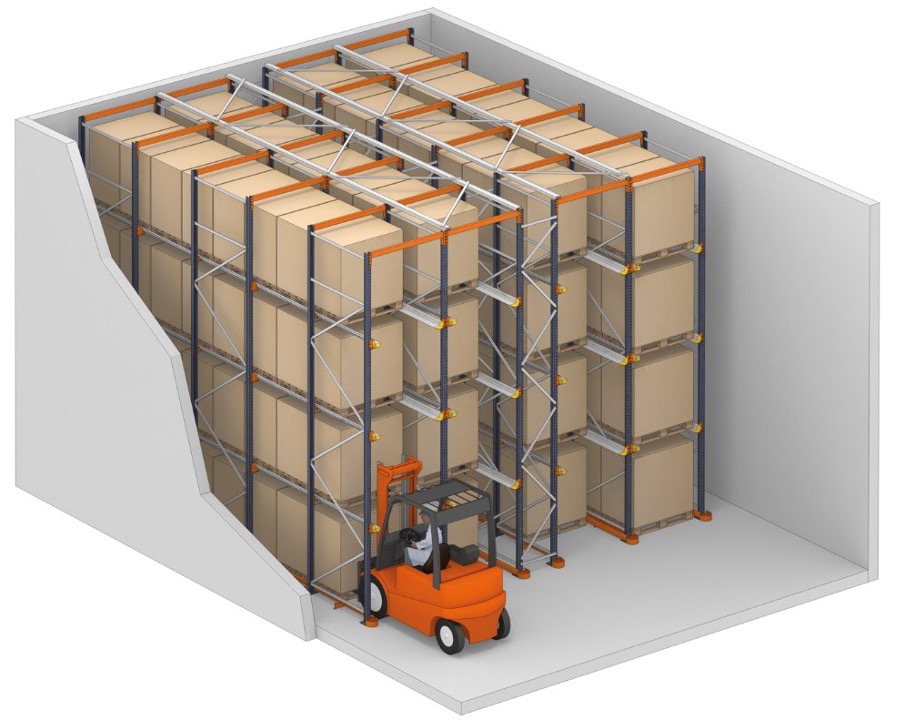
The pallets are stored on “rails” instead of beams. These rails are supported by “arms” connected to the upright frames. The rails are fixed at specific dimensions to accommodate one pallet width and allow for clearance of the lift truck. The depth of the system is based on available space, the quantity, and the size of the pallets that will fit in that space. The height of the system is limited by the pallet height, building clear height and the max lift of the trucks.
Other important design criteria are the pallets and the product (load) on the pallets. Pallets must be quality hardwood (generally with 5 bottom boards) and a consistent size in order to be safely stored in a drive-in rack system. Pallets of poor quality may need the use of a “slave” pallet (placed under the original pallet) in order to be stored in a drive in that system. The product must be positioned square and straight on the pallets to avoid damage to the product and hang-ups in the rack.
Because the lift equipment enters into the rack structure to place and pick inventory, the rack must be protected from contact with trucks. Floor mounted guide rails with entry radiuses, heavy-duty bottom horizontals and rub rails all act to protect the rack system from fork truck abuse. The front upright column should also be reinforced for impact resistance.
Drive-In systems can be the most cost-effective high-density pallet storage solution for large quantities of the same product when that product is not time sensitive.
Pallet Flow
Pallet Flow Racks fully utilize available storage space and ensure the picking aisle has access to stocked pallets. In this first-in, first-out (FIFO) system, pallets are loaded at the top end of the slightly inclined rack.
Then, pallets glide safely and effortlessly at a controlled rate to the front of the storage lane.
These heavy-duty systems are designed for years of trouble-free operations with rugged load-bearing wheels. Inventory rotation is quick and efficient, whether merchandise is moved strictly on pallets or as part of an order picking system. Save space and handling times in your installation.
Pallet Flow Rack Systems come in an infinite variety of layouts, depending on the individual flow rates and order picking requirements. These dynamic racks with rails are highly-suited to frozen-storage warehouses, food distribution or high-volumes of consumer goods.
Gravity flow pallet racks are also good for buffer warehouses and dispatch areas where pallets need to be removed quickly. Every phase of the operation, from how it is fed to required outflows, etc., is carefully considered to provide the most efficient, customized system possible.
Advantages
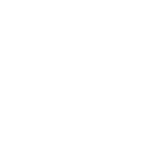
Optimum rotation of products with expiration dates
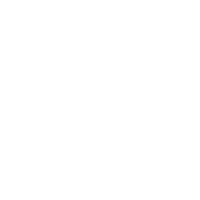
An almost solid volume of usable storage space
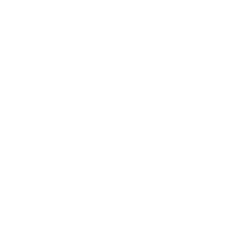
Space, manpower and utilities savings
Pallet Flow Rack System Features
- Reduces Warehouse Cost via automatic gravity flow pallet rotation
- Easy, Efficient Product Loading and Unloading
- First In / First Out (FIFO) Pallet & Product Storage
- Freezer and Cool Room Applicable
- Heavy Duty Long Life Construction
- Reduced Aisle Space By 60 to 70%
- Increased Warehouse Utilization and Space Savings
- Reduced Forklift Damage as pallet or carton flows to the operator or unloading area
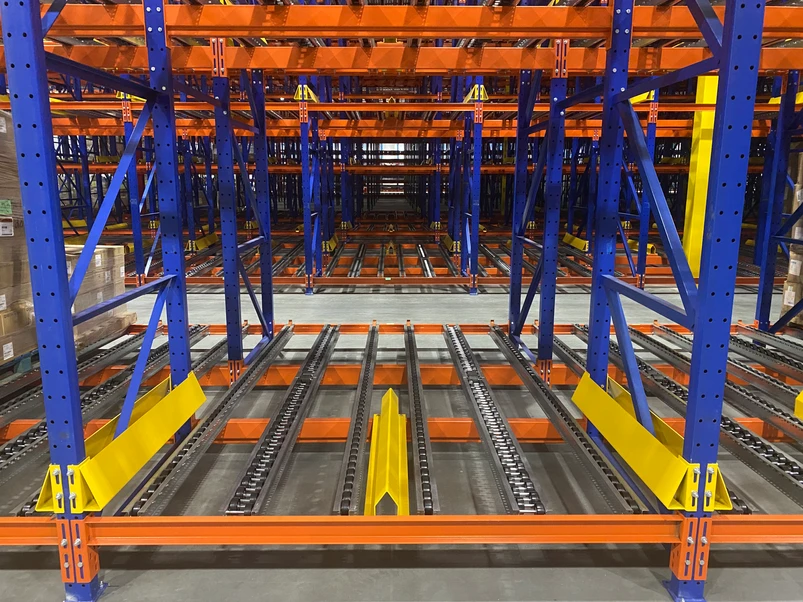
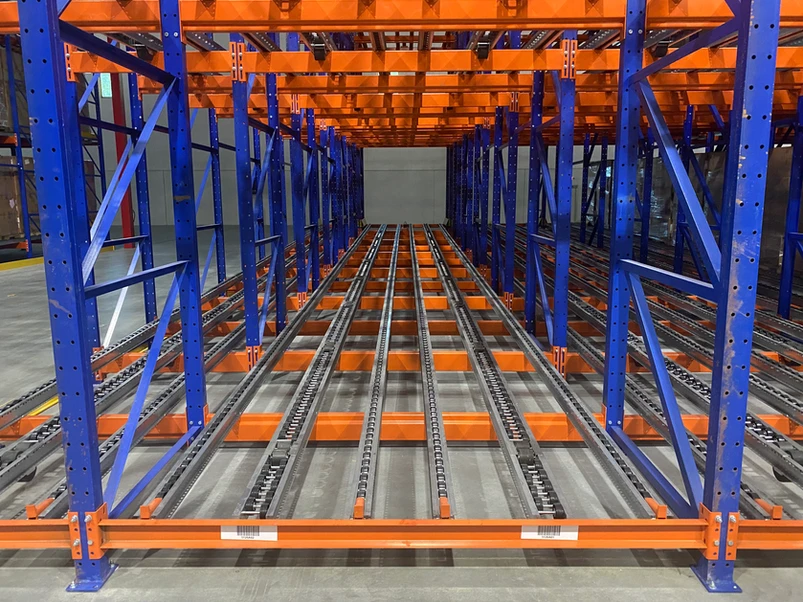
Pallet Flow Rack System Features
- Reduces Warehouse Cost via automatic gravity flow pallet rotation
- Easy, Efficient Product Loading and Unloading
- First In / First Out (FIFO) Pallet & Product Storage
- Freezer and Cool Room Applicable
- Heavy Duty Long Life Construction
- Reduced Aisle Space By 60 to 70%
- Increased Warehouse Utilization and Space Savings
- Reduced Forklift Damage as pallet or carton flows to the operator or unloading area
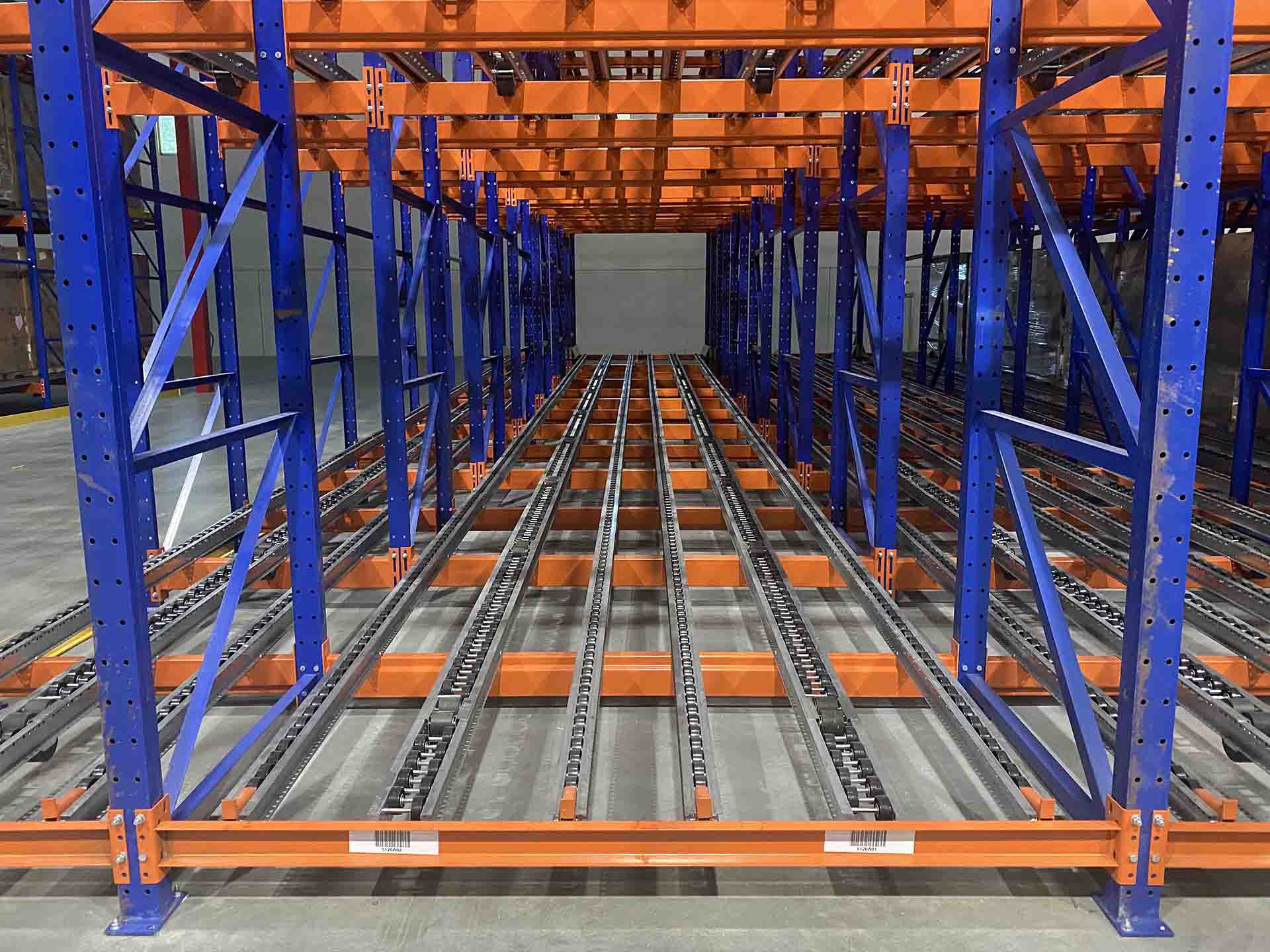
Carton Flow
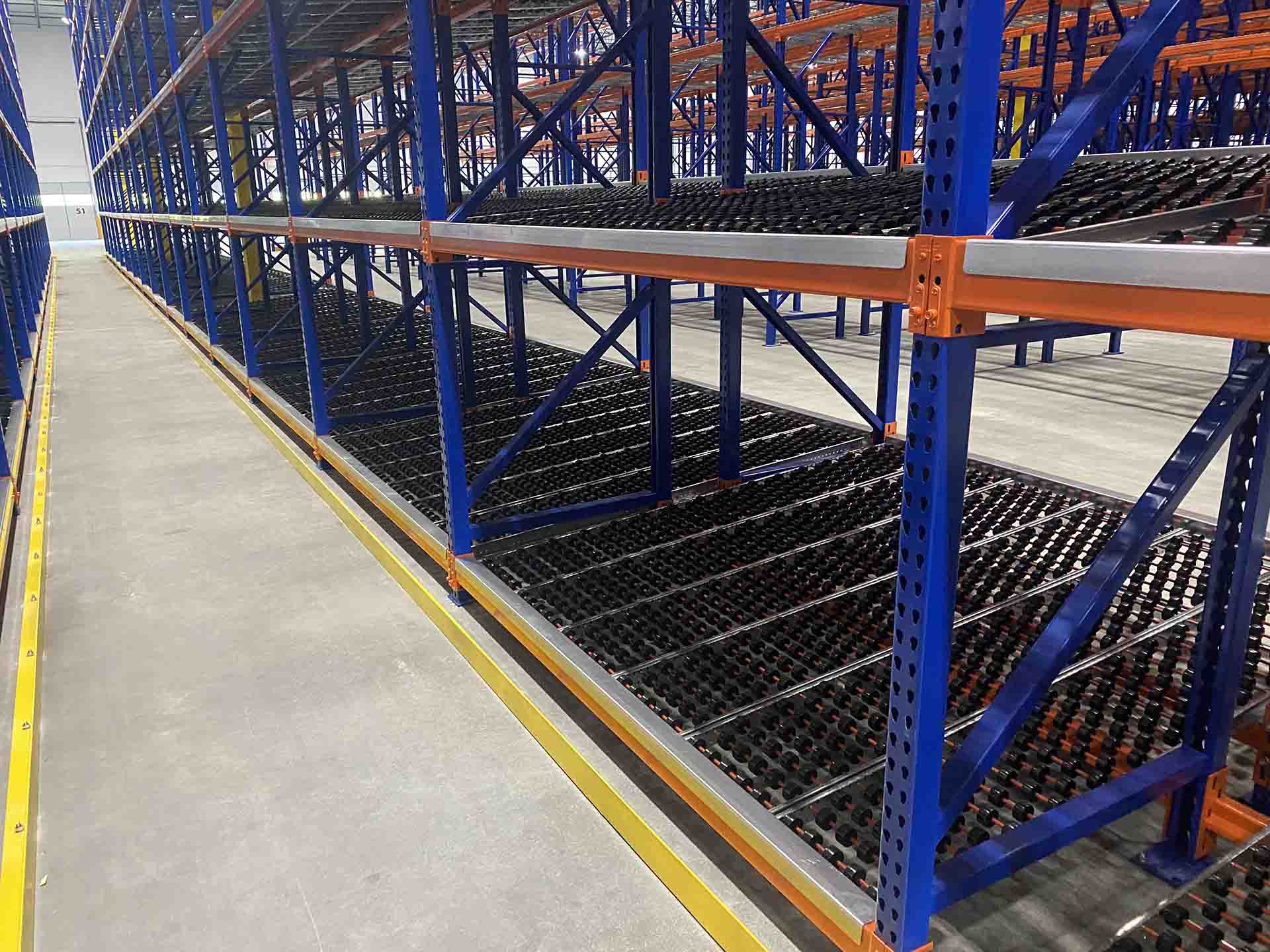
New Carton Flow
- Gravity flow system
- Various roller types are available:
- steel or aluminum tubular rollers
-
plastic or steel skate-wheel rollers
* We can help you identify the right roller based on your product and usage.
- Hand-pick items from open cartons or pick full cartons
- Increases order pickers efficiency and accuracy
- Lanes are loaded from one end and unloaded on the other
- Low maintenance
- Dense FIFO storage
- Many sizes and configurations available!
We Can also Convert Your Existing Pallet Rack to Carton Flow!
Use our flow tracks in your pallet rack for better flow!
Add to any pallet rack – “nests” between beams
Uses standard flow track hangers
Expert installation available
Tubular Roller – Dedicated Lane
Skate-Wheel – Seamless Flow Bed
Keg Flow
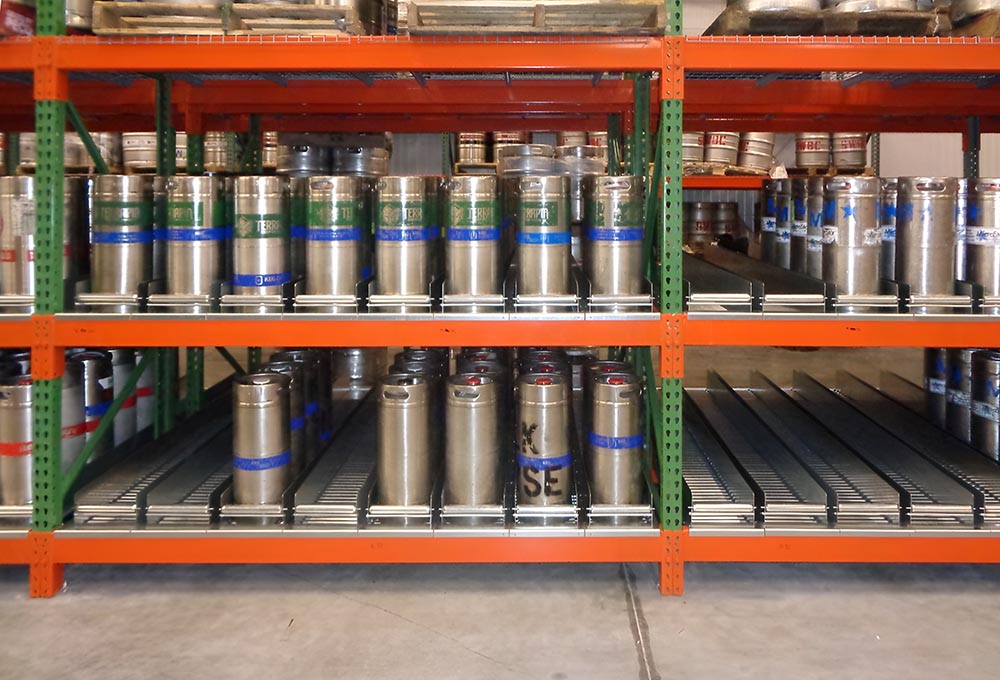
Keg Flow offers an alternative to palletized storage that consolidates floor space, reduces bending, and improves stock rotation. Travel time and mis-picks for order pickers are reduced. Keg Flow allows distributors to offer a greater number of beer variations in a small space.
We offer specialized keg storage solutions for beer distributors to maximize storage space and improve worker efficiency and productivity. Industry Mart has provided keg flow solutions to beer distributors throughout Tennessee.
Features
- Each lane handles both 1/6 and 1/4 slim kegs
- For 1/4 and 1/2 barrels, consult with a product specialist for design
- Same track drops into channel or step beams, interchangeable
- 1-3/8″ diameter heavy duty steel rollers
- Double deep model FIFO stock rotation
- 11-3/4″ wide tracks allow storage of 8 kegs across in a 96-inch wide bay
- High roller stop for easy ergonomic keg “roll-out” and less wear on aluminum kegs
- 6″ common heavy-duty guard rails to keep kegs upright
- Available in single and double-deep lanes
- Impact and slow down skid plates on double deep Keg Flow
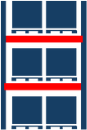
Manufacturers
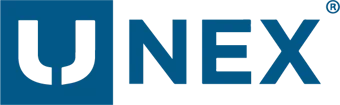
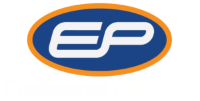
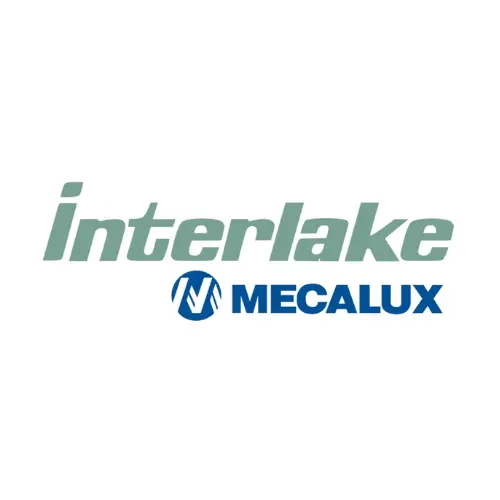
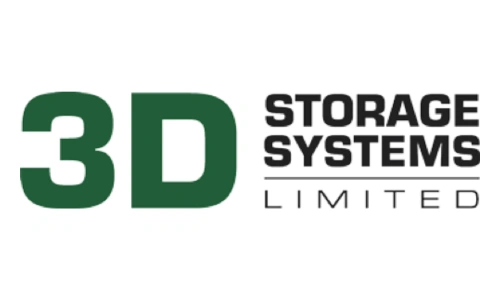
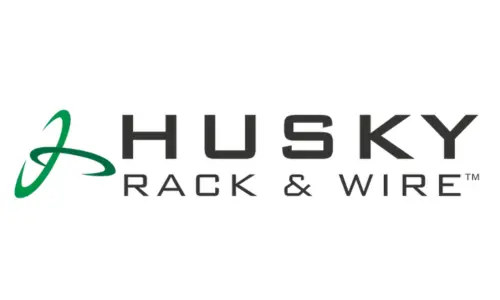
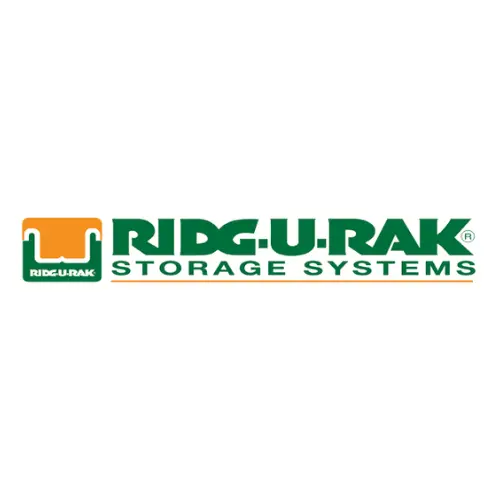
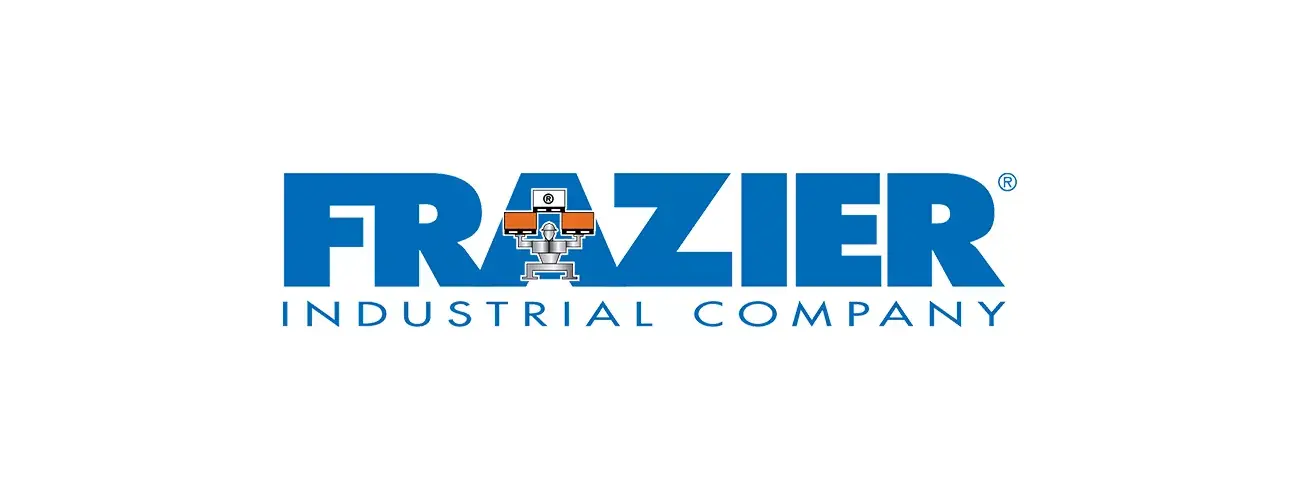
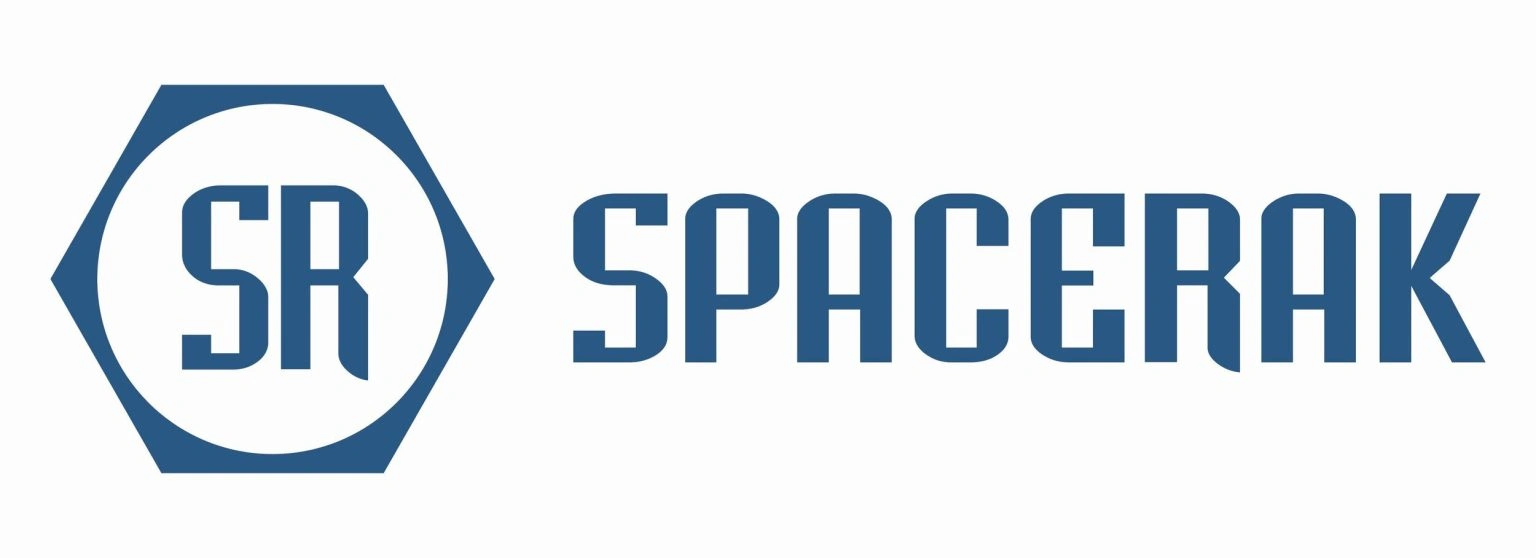
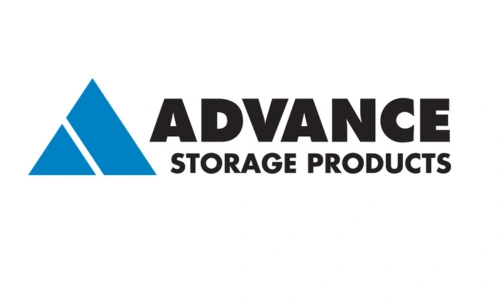
Manufacturer Brochures
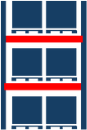